Fiber optic splicing is the process of joining two fiber optic cables to maintain high-speed data transmission. This technique is essential for modern internet and telecommunications networks. In this article, we will discuss the primary methods of fiber optic splicing, the key tools required, and best practices to achieve high-quality splices
Key Takeaways
- Fiber optic splicing is essential for creating durable, low-loss connections in high-speed communication networks, replacing traditional wiring methods.
- The two primary methods of splicing—fusion and mechanical—offer different advantages, with fusion splicing providing stronger and more reliable connections, while mechanical splicing allows for quicker, temporary solutions.
- Proper handling, alignment, and cleaning of fibers, along with high-quality tools, are critical for achieving optimal splice performance and maintaining signal integrity.
Understanding Fiber Optic Splicing
Fiber optic splicing joins two fiber optic cables, creating a continuous data transmission path with a fiber optic splicer. It maintains communication network integrity and efficiency, especially as demand for high-speed internet and telecommunications grows. Fiber optic cable splicing offers permanent or semi-permanent connections, critical for field installations and restoring severed buried cables. Additionally, to effectively connect these systems, technicians must splice fiber optic cables.
The primary reasons for employing fiber splicing include repairing damaged cables and joining different cable types. With fiber optics replacing traditional wiring, splicing becomes vital for reliable and efficient data transmission. This method offers advantages such as lower light loss and better signal quality compared to termination methods, making it a preferred choice in many applications.
The growing telecommunications needs are supported by fiber optic splicing, as fiber optic cables replace coaxial cables for high-speed internet. Mastering this skill is essential to meet the high demands of modern communication networks.
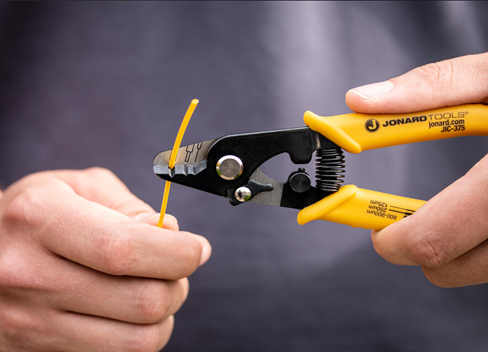
Methods of Fiber Optic Splicing
Fusion and mechanical splicing are the two primary methods of joining fiber optic cables. Each has its advantages and is chosen based on project requirements and constraints. Fusion splicing is generally preferred for permanent connections due to its lower connectivity loss and the strength of the joint, making it ideal for long-term use.
Mechanical splicing uses a device to align fibers without melting, primarily for quick restoration and temporary connections. Budget and project longevity often influence the choice between mechanical splice and fusion splicing, with mechanical splicing offering quicker temporary solutions.
Fusion Splicing Process
Fusion splicing heats and melts fiber ends using an electric arc, resulting in low loss and durable connections. The fusion splicer aligns and fuses the ends with heat. This process ensures that the fibers are perfectly aligned, providing a seamless connection that minimizes signal loss.
Typical insertion loss for fusion splicing is around 0.1 dB, without creating Fresnel reflections, ensuring high-quality splices. It’s commonly used for long outside plant cable runs and high data rate connections.
Favored for its reliability and longevity, fusion splicing is the preferred choice for permanent installations.
Mechanical Splicing Process
Mechanical splicing aligns and holds optical fibers using an assembly and index matching fluid, without heat. It uses an assembly and index matching gel to secure the fibers. Mechanical splicing is small, easy to use, and suitable for quick repairs or permanent installations.
The index-matching gel reduces Fresnel reflections or losses at the splice connection, enhancing light transmission. While not outperforming fusion splices, mechanical splices offer better performance than mated connector pairs.
Simpler and less expensive, mechanical splicing is generally used for temporary connections due to lower reliability compared to fusion splicing.
Key Factors Influencing Splice Performance
Performance of a fiber optic splice is influenced by intrinsic factors related to fiber variations and extrinsic factors concerning external conditions. Intrinsic factors like differences in refractive index and concentricity can significantly affect splice quality, leading to potential signal loss. Extrinsic factors like proper alignment and cleanliness during splicing are crucial for minimizing insertion loss.
Proper handling of fiber cables, avoiding bends or twists beyond their bend radius along the fiber axis, is necessary to maintain splice integrity. Both intrinsic and extrinsic factors are vital for high-quality splices, and understanding these influences helps optimize the splicing process.
Intrinsic Factors
Intrinsic factors that affect splice performance include variations in the numerical aperture (NA) and core diameters of optical fibers. Loss may occur if the transmitting fiber’s NA is larger than the receiving fiber’s NA. Differences in core diameters between fibers can also result in light loss in the cladding, particularly in multimode fibers.
Manufacturing imperfections can cause concentration variations in optical fibers, leading to light loss. Understanding these intrinsic factors is crucial for achieving optimal splice quality.
Extrinsic Factors
Extrinsic factors affecting splice quality include alignment conditions and contamination. Lateral misalignment increases splice loss by allowing light from the transmitting fiber to enter the cladding of the receiving fiber. End separation, a gap between transmitting and receiving fibers, leads to Fresnel reflection losses.
Contamination, like microscopic particles on the fiber, can increase splice loss and degrade signal quality. Proper alignment and cleanliness are critical for maintaining high-quality splices and minimizing signal loss.
Tools and Equipment for Fiber Optic Splicing
- Fusion Splicer: Aligns fibers and uses an electric arc to create a permanent connection; modern models include displays and cameras for precise alignment.
- Fiber Cleaver: Critical for achieving precise cleaving, enhancing fusion splicing quality and reducing signal loss.
- Mechanical Splicing Connectors: Hold fibers in alignment for a quick and effective splicing solution.
- Cleaning Tools: Include alcohol and lint-free wipes to ensure fiber ends are free from contaminants.
- Fiber Strippers: Used to remove protective coatings from the fiber before splicing.
- Splice Protectors: Safeguard spliced connections, maintaining durability and longevity.
- Skill and Expertise: A high degree of proficiency and the use of specialized tools are crucial for successful fiber optic splicing.
Steps to Perform Fusion Splicing
- Remove Protective Coating: Use a fiber optic stripper to carefully remove the protective coating from the fiber cables.
- Clean the Fiber: Clean the exposed fibers with alcohol and lint-free wipes to remove contaminants.
- Cleave the Fiber: Use a precision fiber cleaver to achieve a clean and precise cut, which is essential for effective splicing.
- Position the Fibers: Place the fibers in the fusion splicer, ensuring they are correctly aligned.
- Splice the Fibers: Activate the fusion splicer to join the fibers using an electric arc, creating a permanent connection.
- Apply Protective Sleeve: Cover the splice with a heat-shrink protective sleeve and use a heater to secure it in place.
- Test the Splice: Verify the splice quality by measuring signal loss using an optical power meter or similar tool.
- Maintain Equipment: Regularly clean and calibrate the splicing machine to ensure consistent performance and reduce errors.
Steps to Perform Mechanical Splicing
- Prepare the Fibers: Remove the protective coatings from the fibers using a fiber optic stripper, ensuring a clean surface.
- Clean the Fiber Ends: Wipe the exposed fibers with alcohol and lint-free wipes to eliminate dust and contaminants.
- Cleave the Fibers: Use a fiber cleaver to achieve a relatively clean cut; while precision is less critical than in fusion splicing, a clean cleave is still important.
- Align the Fibers: Place the fiber ends in the mechanical splice device, ensuring proper alignment for effective signal transmission.
- Apply Index Matching Gel: Use index matching gel to minimize reflection and loss at the splice point.
- Secure the Connection: Tighten or lock the mechanical splice device to hold the fibers securely in place.
- Place in Splice Tray: Organize the spliced fibers in a splice tray to prevent movement or damage.
- Seal in Splice Closure: Protect the splice from moisture and environmental factors by sealing it inside a splice closure.
- Test the Splice: Verify the splice's performance by measuring signal loss or conducting continuity checks.
Troubleshooting Common Splicing Issues
Common splicing issues can significantly impact splice quality and overall signal transmission. Cleaning supplies like alcohol and wipes are essential for preparing fibers before splicing to avoid contamination. Testing splice quality with tools like power meters or OTDRs verifies signal strength and loss for optimal data transmission.
A splice can be reworked to ensure optimal transmission quality, but only up to twice. Understanding and addressing common splicing issues helps maintain high-quality splices and ensure reliable data transmission.
Cleave Angle and Length
Improper cleave angle can lead to poor fiber alignment and increased splice loss. Cleave length must be precise to prevent excess splice loss during fusion splicing. A proper cleave angle is crucial for high-quality fiber optic splices.
Cleave angle and length significantly influence overall splice performance and signal integrity. Paying close attention to these factors ensures better splice quality and minimizes signal loss.
Contamination and Bubbles
Contamination on optical fibers can exceed attenuation requirements, especially in singlemode fiber. High-loss splices in fusion splicing can occur due to misalignment caused by microscopic dirt particles. Cleaning fiber ends with lint-free wipes and appropriate solutions eliminates contaminants that could affect signal quality.
Bubbles in fiber optic splicing can be caused by dirt or entrapped air. Preventing bubbles in a fusion splice requires following specific steps during the process. After cleaning the fibers, avoid touching contaminated surfaces to maintain cleanliness.
Benefits and Challenges of Fiber Optic Splicing
Fiber optic splicing offers significant advantages for deploying high-speed communication networks. Fusion splicing creates low-loss connections, providing permanent solutions with higher tensile strength. Ideal for long-distance communication networks, this method offers durability and minimal signal loss.
However, fiber optic splicing presents challenges, including susceptibility to environmental factors and the need for specialized tools and delicate processes. Mechanical splicing, while faster and more convenient, suits temporary solutions but may pose long-term performance issues.
Overall, fiber optic splicing delivers superior networking performance but requires careful consideration of associated challenges.
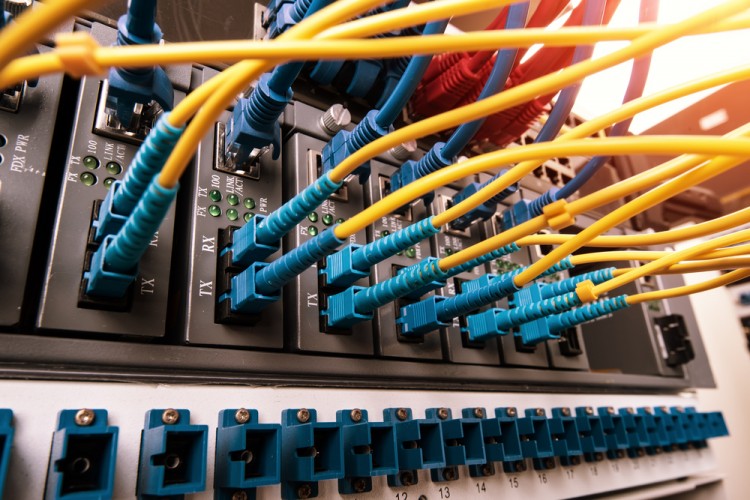
Best Practices for High-Quality Splicing
Achieving high-quality splices requires the use of precision tools like cleavers, which are vital for ensuring low attenuation during splicing. The quality of cleavers significantly influences the effectiveness of the splicing process, making it essential to invest in good equipment. Effective cleaning methods for fibers, including using lint-free wipes with isopropyl alcohol, are also crucial for maintaining splice integrity.
Documenting issues and the steps taken during the splicing process can provide valuable insights for future troubleshooting. Cleave length directly affects splice loss, so ensuring accurate cleaves is imperative. Practice and adherence to best practices are essential for achieving better splicing results, ultimately leading to more reliable and efficient fiber optic networks.
Pro Tip: Regularly inspect and maintain your splicing equipment to ensure optimal performance. Dirty or damaged cleaver blades and splicing tools can compromise the precision of your splices, leading to higher loss rates. Replace consumables like cleaver blades as recommended by the manufacturer to sustain consistent results.
Summary
In summary, mastering fiber optic splicing is crucial for maintaining the integrity and efficiency of modern communication networks. By understanding the different methods of splicing, the factors influencing splice performance, and the importance of using the right tools and techniques, you can achieve high-quality splices with minimal signal loss. Whether you are performing fusion splicing or mechanical splicing, attention to detail and adherence to best practices are key to success.
As the demand for high-speed internet and reliable telecommunications continues to grow, the role of skilled fiber optic technicians becomes increasingly important. By investing in the right training and equipment, and by following the tips and techniques outlined in this guide, you can excel in the field of fiber optic splicing and contribute to the advancement of modern communication networks.
Why Choose Phoenix Communications for Fiber Optic Splicing in Shrewsbury, MA
Phoenix Communications Inc. is the top choice for fiber network contracting in Shrewsbury, MA, offering expert fiber optic splicing services with unmatched precision and efficiency. Our certified technicians use the latest tools and techniques, specializing in both fusion and mechanical splicing to ensure robust and reliable connections. With extensive industry experience, we handle complex projects seamlessly, minimizing downtime and maximizing network performance.
Trust Phoenix Communications for your fiber optic needs and experience superior service. Our representatives are standing by to discuss your needs. Contact Phoenix Communication Inc. today to establish an immediate response for your next outage.
Frequently Asked Questions
What is fiber optic splicing?
Fiber optic splicing is the critical process of joining two fiber optic cables to ensure a seamless data transmission path, which is vital for the integrity and efficiency of communication networks.
What are the main methods of fiber optic splicing?
The primary methods of fiber optic splicing are fusion splicing, which employs heat to permanently join the fibers, and mechanical splicing, which aligns fibers without the need for melting. Both methods ensure effective connections in fiber optic networks.
What tools are essential for fiber optic splicing?
Essential tools for fiber optic splicing include a fusion splicer, fiber cleaver, fiber optic stripper, cleaning supplies, and splice protectors. These tools ensure precision and effective connections, which are critical for optimal fiber performance.
What are the key factors affecting splice performance?
The key factors affecting splice performance include intrinsic factors such as fiber variations and extrinsic factors like alignment and cleanliness. Ensuring both aspects are optimized is crucial for achieving the best splice quality.
What are the benefits of fusion splicing?
Fusion splicing offers low loss connections and high tensile strength, making it an ideal solution for long-distance communication networks. This ensures a reliable and durable fiber optic connectivity.