Want to ensure your cable installation is done right? This article breaks down the top practices to follow for reliable and durable cable projects. From initial planning to final protection, get the insights you need to succeed in cable installation.
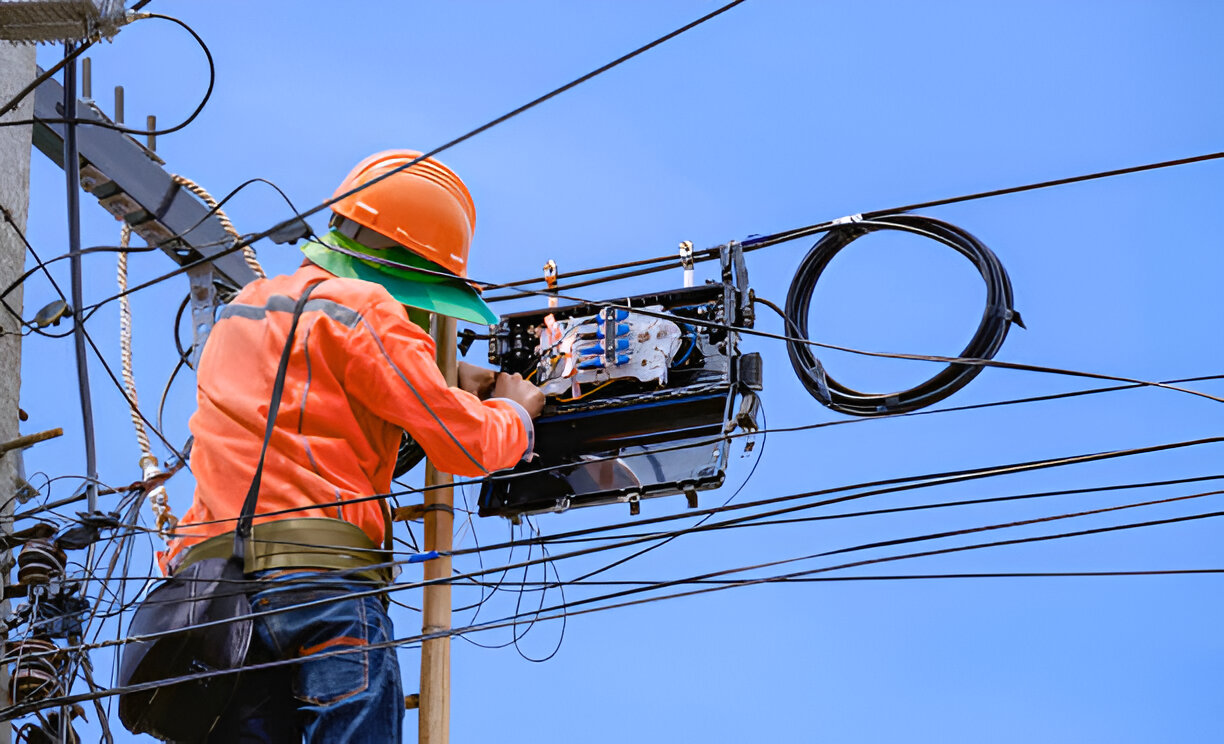
Key Takeaways
- Effective cable installation requires meticulous planning, seabed preparation, and the use of appropriate cable laying techniques to ensure performance longevity.
- Post-installation testing and certification are crucial for verifying cable integrity and ensuring compliance with safety and performance standards.
- Emerging trends, such as the adoption of fiber optic cables and smart installation tools, are transforming the cable installation landscape, enhancing efficiency and functionality.
Essential Steps in Cable Installation
Installing cables in demanding environments, such as offshore wind farms, requires a systematic approach to ensure durability and performance. The key steps include preparation, laying, and protection, all of which are essential for reliable and long-lasting installations.
Cable manufacturers specify guidelines, such as minimum bend radius and tensile limits, to prevent damage during handling and installation. Proper planning and design are critical, incorporating site assessments and regulatory compliance. Seabed preparation follows, clearing obstacles and optimizing the terrain for secure cable laying.
Advanced technologies, including automation and AI, enhance efficiency by providing real-time feedback, minimizing errors, and ensuring cables remain protected and perform as expected.
Planning and Design
Planning and design are the cornerstones of any successful cable installation project. Technical considerations ensure the installation meets performance expectations and complies with local regulations. Project certification verifies that the design adheres to specific site conditions and regulatory requirements.
Independent certification during the operational phase mitigates risks and ensures ongoing compliance. Using rocks to protect cables around turbine bases and burying cables in soft sediment to depths of up to 10 meters are some strategies employed to safeguard the power conduit installation, for example.
Cutting chainflex cables to length and installing them without prior relaxation enhances performance.
Seabed Preparation
Seabed preparation is a critical step in the installation process. Clearing seabed obstacles ensures a smooth path for cable laying, minimizing potential delays and issues. Cutting and burying out-of-service cables within the corridor prevents interference with new installations.
Optimal burial depths for cables typically range around 3 meters, with soft sediment being the most favorable soil condition. However, hard soils, bedrock, slopes, and proximity to structures can pose challenges that may prevent adequate burial.
Thorough seabed preparation ensures the success and longevity of the cable installation.
Cable Laying Techniques
The actual laying of cables involves various techniques designed to protect and secure the cables. Installing one cable per conduit is a standard practice to ensure proper conduit fill and protect the integrity of the installation. Trenching involves excavating a trench to lay the cable below the seabed surface. This method ensures the cable is buried at an appropriate depth, protecting it from external damage.
Other methods use specialized cable installation tools and techniques tailored to the project’s specific requirements. These methods ensure the cables are laid efficiently and securely, maintaining their integrity and performance over time.
Cable Handling and Storage
Best Practices for Handling
Proper handling of cables is crucial to prevent damage and ensure safe installation. Here are some best practices for handling cables:
- Handle with Care: Always handle cables with care, avoiding twists, bends, and kinks that can damage the outer insulation and conductors. Mishandling can lead to compromised performance and increased risk of failure.
- Use Appropriate Equipment: Utilize cable handling equipment, such as cable reels and cable drums, to minimize manual handling and reduce the risk of damage. These tools help maintain the integrity of the cables during transportation and installation.
- Secure During Transportation: Ensure that cables are properly secured during transportation to prevent movement and potential damage. Unsecured cables can suffer from abrasions and other forms of mechanical stress.
- Organize with Cable Ties and Clips: Use cable ties and cable clips to keep cables organized and prevent tangling. This practice not only protects the cables but also makes the installation process more efficient.
- Avoid Extreme Conditions: Keep cables away from extreme temperatures, moisture, or chemicals that can damage the insulation and conductors. Exposure to harsh conditions can degrade the cable’s performance and lifespan.
Storage Guidelines
Proper storage of cables is essential to maintain their quality and prevent damage. Here are some storage guidelines for cables:
- Optimal Storage Environment: Store cables in a dry, cool, and well-ventilated area, away from direct sunlight and moisture. These conditions help preserve the cable’s outer insulation and overall integrity.
- Use Storage Racks and Reels: Utilize cable storage racks and cable reels to keep cables organized and prevent tangling. Proper organization ensures that cables are easily accessible and reduces the risk of damage.
- Label and Identify: Ensure that cables are properly labeled and identified to prevent mix-ups and confusion. Clear labeling helps in quick identification and reduces the chances of errors during installation.
- Protective Covers: Store cables in their original packaging or use protective covers to prevent damage and contamination. Protective covers shield the cables from dust, dirt, and other potential contaminants.
- Avoid High Traffic Areas: Refrain from storing cables in areas with high foot traffic or where they may be subject to mechanical stress. Keeping cables in low-traffic areas minimizes the risk of accidental damage.
Cable Protection Measures
Protecting cables after installation ensures their longevity and performance. Burial, the primary method for cable protection, safeguards cables from potential damage caused by environmental factors and human activities. Effective protection measures maintain the operational integrity of the cables.
Alongside burial, various alternative protection methods enhance cable security. These methods are useful in challenging environments where burial alone may not provide sufficient protection.
Cable Burial
Cable burial is the most common and effective method for protecting cables. Simultaneous lay and burial techniques securely embed the cables in the seabed. Burial depth is influenced by soil type and its cut-ability, which significantly affect installation efficiency.
Recommended burial depths range from 1 to 1.7 meters, reaching up to 3 meters or even 10 meters in soft sediment under shallow water conditions. Soil types like cohesive sands, hard clays, and stiff soils impact burial process effectiveness.
Alternative Protection Methods
When burial is not feasible or sufficient, alternative protection methods are used. Concrete mattresses are reliable for protecting cables at crossings. Designed with tapered edges to accommodate fishing gear, these mattresses provide additional security.
Articulated split pipes and Uraduct systems protect against surface damage and abrasion during cable installation. Rock filter bags effectively protect against scour and secure cables at crossings.
Tools Required for Cable Installation
The success of any cable installation project relies on using appropriate tools. Essential cable installation tools include cable pullers, wire cutters, and crimping tools designed for safe and efficient handling. Jet plows and trenching machines are indispensable for burying cables.
Tools like boulder plows and boulder picks remove seabed obstacles, ensuring a clear path for cable installation. Cable Lay Vessels (CLVs) lay cables on the seabed, while tugboats or laying vessels assist in the cable pull-in process.
Punch Down Tools
Punch down tools ensure reliable connections in cable installations. These tools come in various types, including standard and impact punch down tools, each designed for specific wiring setups and connector styles.
They connect wires to terminals in patch panels and network sockets, ensuring secure and reliable connections. The right punch down tool significantly enhances the speed and accuracy of the installation process.
Understanding Cable Specifications
Understanding cable specifications is fundamental to successful installation. Proper techniques greatly enhance the lifespan and effectiveness of cables. Effective planning considers technical specifications to ensure cables meet performance standards.
The trend towards miniaturization has led to specialized cable designs integrating multiple functions into single cables. Industry 4.0 has increased demand for modular connectors that enable frequent reconnections without compromising reliability.
Minimum Bend Radius
The minimum bend radius is a critical specification during cable installation. This radius indicates the minimum curve within which a cable can be bent without damage, maintaining its integrity and performance.
Bending a cable beyond its specified radius can cause material thinning, cracking, and loss of electrical properties. It can also damage the insulation, compromising the cable’s long-term reliability. The bending radius is typically expressed as a multiple of the cable’s outer diameter.
Cable Tension and Pulling
Proper cable tension and pulling techniques prevent damage during installation. Excessive pulling forces can lead to premature cable failures, typically within a few years of installation. Performing cable pull calculations prior to installation minimizes potential damage by determining appropriate cable sizes and routing.
Reducing bends in the cable run lowers side wall bearing pressure, crucial for maintaining cable integrity. Leaving adequate slack in the cable, typically 20-30 feet, ensures easier handling and reduces installation tension. Specific tensile ratings indicate the maximum allowable cable tension, which is crucial.
Safety and Documentation
Safety Protocols
Safety protocols are essential to prevent accidents and injuries during cable installation. Here are some safety protocols to follow:
- Training and PPE: Ensure that all personnel involved in cable installation are properly trained and equipped with personal protective equipment (PPE). Proper training and PPE are the first lines of defense against potential hazards.
- Regular Safety Inspections: Conduct regular safety inspections to identify potential hazards and take corrective action. Routine checks help maintain a safe working environment and prevent accidents.
- Safety Signs and Warning Labels: Use safety signs and warning labels to alert personnel of potential hazards and dangers. Clear signage ensures that everyone is aware of the risks and takes necessary precautions.
- Proper Grounding and Bonding: Ensure that all cables are properly grounded and bonded to prevent electrical shock. Proper grounding is crucial for the safety of the installation and the personnel involved.
- Lockout/Tagout Procedures: Follow proper lockout/tagout procedures to prevent accidental start-up of equipment. These procedures are vital for ensuring that equipment is safely de-energized during maintenance and installation activities.
By adhering to these best practices and safety protocols, you can ensure a successful and safe cable installation process. Proper handling, storage, and safety measures not only protect the cables but also enhance the overall efficiency and reliability of the installation.
Post-Installation Testing and Certification
Post-installation testing and certification ensure installed cables comply with specified performance criteria. This process ensures operational reliability. Testing and certification mitigate potential operational risks and ensure the installation meets defined performance benchmarks.
Various tests and certification tools verify the integrity and performance of installed cables. These tests and tools ensure the installation adheres to safety and quality standards, guaranteeing long-term reliability.
Types of Tests
Cables undergo several tests to validate their integrity before and after installation. These include pre-qualification, type testing, and routine electrical testing. Verification tests confirm the installation meets specified requirements, while qualification tests assess performance under various conditions.
Electrical tests, such as insulation resistance and time-domain reflectometry, confirm the integrity of cables post-installation. These testing stages are crucial for ensuring long-term cable performance and reliability.
Certification Tools
Manufacturer-approved tools ensure accurate measurements and compliance with safety and quality standards during certification. These tools monitor and verify installation practices and component integrity.
The certification process assesses the manufacturing quality of components at offshore wind farms, ensuring they meet necessary standards. Specialized tools handle and check components, ensuring they adhere to specified criteria.
Summary
The successful installation of cables hinges on meticulous planning, effective protection measures, and the use of appropriate tools. The essential steps of cable installation include thorough planning and design, careful seabed preparation, and the application of reliable cable laying techniques. Each step is critical in ensuring that the cables perform as intended and have a long service life.
Protecting cables through burial and alternative methods like concrete mattresses and articulated split pipes is vital for maintaining their integrity. Understanding cable specifications, such as minimum bend radius and proper tension, further ensures that cables are installed correctly and function optimally. Post-installation testing and certification are indispensable for verifying the performance and reliability of the installed cables.
As we look to the future, emerging trends and technologies, such as fiber optic cables and smart installation tools, promise to revolutionize the industry. Staying updated with these advancements is essential for professionals to deliver high-quality installations and meet the growing demands for connectivity. Embracing these best practices will not only enhance efficiency but also pave the way for a more connected and technologically advanced future.
Contact Phoenix Communications Inc for Fiber Optic Needs in Shrewsbury, MA
Phoenix Communications Inc. is the leading fiber optic contractor in New England, known for fostering strong partnerships with telecommunications companies and local enterprises. Our commitment to quality and innovation ensures top-notch cable installation services tailored to your needs.
Enhance your telecommunications infrastructure with Phoenix Communications Inc. Contact us today to experience superior connectivity and expert service.
Frequently Asked Questions
Why is planning and design crucial in cable installation?
Planning and design are crucial in cable installation to ensure adherence to technical specifications and local regulations, which directly impacts the optimal performance and longevity of the cables. This approach minimizes risks and helps achieve reliable and efficient installations.
What are the primary methods for protecting installed cables?
The primary method for protecting installed cables is burial, which effectively safeguards them from environmental and human-induced damage. For challenging environments, additional protections such as concrete mattresses and articulated split pipes can be employed.
What tools are essential for cable installation?
Essential tools for cable installation include cable pullers, wire cutters, crimping tools, jet plows, trenching machines, and Cable Lay Vessels (CLVs) to ensure a safe and efficient process.
Why is understanding the minimum bend radius important?
Understanding the minimum bend radius is crucial to prevent damage to cables during installation, as exceeding this radius can result in material thinning, cracking, and a loss of electrical properties, ultimately compromising the cable's integrity and performance.
What future trends are shaping the cable installation industry?
The future of the cable installation industry is being shaped by the rise of fiber optic cables and the adoption of smart installation tools, which significantly enhance efficiency and accuracy in the installation process. Embracing these trends will be essential for staying competitive in the evolving market.